Talk:Stirling engine
This is the talk page for discussing improvements to the Stirling engine article. This is not a forum for general discussion of the article's subject. |
Article policies
|
Find sources: Google (books · news · scholar · free images · WP refs) · FENS · JSTOR · TWL |
![]() | This ![]() It is of interest to multiple WikiProjects. | |||||||||||||||||||||||||||
|
|
||||||
Lede image
[edit]The image at the article head conveys nothing. It is too dark and even when animated it explains nothing about the working or history of the Stirling engine. A better image needs to be found. We need one that conveys the working with being confusing.Lumos3 (talk) 14:42, 8 April 2022 (UTC)
- I favour this image because 1) it shows the essential simplicity of the design 2) it conveys the timeframe of the design which goes all they way to the industrial revolution. 3)It has warm attractive colours of brass and engineering red. It attracts the reader to look into the subject. Lumos3 (talk) 14:51, 8 April 2022 (UTC)
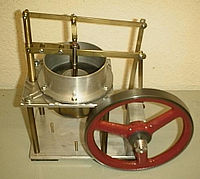
pressure
[edit]contrary to what one reads all over the internet stirling engines do not go below atmospheric pressure and suck the power piston back in if the power piston has one side in the open air.
in another part of the article it is correctly stated that the flywheel provides the work for compressing the working fluid.
imagine an engine sitting ready for work, start heating the hot end, engine runs, the cold end must be above ambient temperature to transfer heat to the atmosphere and so the pressure of the working fluid must be above atmospheric. Froggarana (talk) 16:10, 23 August 2020 (UTC)
- Your argument is not convincing because the working piston's movement means the total volume is higher than at the start of the cycle. So the conditions you describe do not rule out a pressure of <1atm at the phase within 90° of max volume. 2.100.227.229 (talk) 11:21, 1 May 2024 (UTC)
While the above would be true for a perfectly sealed engine, in practice small leaks mean that the average internal pressure will stabilise to atmospheric, therefore the pressure will indeed be below atmospheric for part of the cycle.Pv=mrt (talk) 18:48, 9 July 2021 (UTC)
by what means does the working fluid leak from a region which you say is below atmospheric to a region at higher pressure ie atmospheric ? 37.1.170.203 (talk) 10:53, 7 October 2021 (UTC)
Single source in section - hotairengines.com
[edit]This entire section depends upon a single source. While this dissertation seems well laid out, the entire website is the work of a single person, Isaac Woerlen, whose only point of contact is through LinkedIn. The author seems greatly concerned with the environmental impact of all types of engines, and he shows a distinct bias towards hot air energy.
Another problem here is that the text of this section follows very closely on what the website presents:
The first engine of this kind which, after various modifications, was efficiently constructed and heated, had a cylinder of 12 inches (approx. 30 cm) in diameter, with a length of stroke of 2 feet (approx. 61 cm), and made 40 strokes or revolutions in a minute (40 rpm). This engine moved all the machinery at the Dundee Foundry Company's works for eight or ten months, and was previously ascertained to be capable of raising 700,000 lbs. one foot in a minute (approx. 21 HP).
—hotairengines.org
The first engine of this kind which, after various modifications, was efficiently constructed and heated, had a cylinder of 30 centimetres (12 inches) in diameter, with a length of stroke of 60 centimetres (2 ft), and made 40 strokes or revolutions in a minute (40 rpm). This engine moved all the machinery at the Dundee Foundry Company's works for eight or ten months, and was previously found capable of raising 320,000 kg (700,000 lbs) 60 cm (2 ft) in a minute, a power of approximately 16 kilowatts (21 horsepower).
—Stirling_engine#Early_hot_air_engines
I've started an RfC about this source. I'd like to hear thoughts on the rest. — Myk Streja (beep) 21:40, 31 December 2020 (UTC)
- That text appears in the 1845 engineering journal where Stirling published his research. Copyright-wise, it is probably public domain now. It should be presented as a quote here. Thundermaker (talk) 15:07, 2 January 2021 (UTC)
Agree Re. single questionable source, plus the 'early hot air engines' section was intended to be a brief round-up of precursors to Stirling's work. TBF, this article seems to have become a bit of a mess since I last looked in!Pv=mrt (talk) 18:31, 9 July 2021 (UTC)
The Beta-Configuration blatantly, avoidably, departs from the Stirling-Cycle.
[edit]As for the Beta-Configuration, the whole point of the Stirling is that the air expands at the max temp, with heat being added to keep it there, and is compressed at the min temp, with heat being removed to keep it there. But, in the Beta-Configuration, the expanding air has to go through, and be in contact with, the heat-sink. Having the heat-sink remove heat from the expanding air wasn't part of the plan. The Alpha-Configuration doesn't have that fault.
- Here's a possible (at least partial)answer to my objections:
- When the air in the hot-space expands: Though the air expanding through the regenerator (which evidently was around the displacer in Stirling's patent) is being cooled by the regenerator, and though the air expanding into the cool region is being cooled...most of the volume of the air is in the large (due to the position of the displacer) hot-space, and therefore most of the air is not being cooled by the regenerator and the cold-space. So the expansion isn't so seriously hindered by that cooling by the regenerator and the cold-space.
- That mitigates the problems I spoke of, though it doesn't eliminate them. It seems to me that the Alpha Stirling would be more efficient, because it doesn't have that problem, not having to try to use those spaces for dual-purpose.
- Maybe the inefficiency of Beta & Gamma could be reduced a bit:
- 1. Maybe it would be feasible for the heat-sink surface to be arranged so that, when the displaer is at or near its top position, it covers all or most of the heat-sink surface. ...so that the hot air expanding into the top section won't be (as much) chilled by the heat-sink surface.
- 2. Why not have an outward-flare in the diameter of the displacer's cylinder, a little below the level where the bottom of the displacer is when the displacer is at the top. ...so that, when the displacer is up, having sent the air down to the hot-space, the bottom of the displacer will be in the flared section of its cylinder, thereby leaving a wider space around it, through which for the hot air from below to expand past the displacer without being chilled by the regenerator.
- In that way, as well, of course the regenerator won't be heated by that expanding air, thereby leaving the regenerator more effective when it's later needed to cool the air being displaced upward to the cold-space.
- Someone who collects & sells, and maybe makes Stirlings has said that he finds that the Alphas tend to be more powerful. An Alpha was what was used in NASA's Stirling Chevy Celebrity, which beat the original Otto Celebrity in 0 to 60.
- Of course, if transportation-energy-use, as measured by gallons of fuel purchased, were alloted equally, then a driver could choose any of the ultra-clean-burning external-combustion engines--Stirling (Alpha, Beta, or Gamma) or Rankine (Steam or Freon) based on their price, and based on how much mileage they'd give, with the alloted gallons of fuel.
- — Preceding unsigned comment added by 71.84.136.105 (talk) 01:24, 17 January 2021 (UTC)
- Someone said that there are no examples of the Alpha-Configuration being used. Maybe not in table-models, but when, in or near 1986, a NASA team built an automotive Stirling, and installed it in a Chevy Celebrity, a fully-capable and practical prototype that did 0-60 faster than the ordinary Otto Celebrity, and was 33% more efficient, their Stirling-engine used the Alpha-Configuration. — Preceding unsigned comment added by 71.84.136.105 (talk) 15:04, 4 January 2021 (UTC)
Efficiency compared to that of an internal combustion engine
[edit]The article says:
"Stirling engines by definition cannot achieve total efficiencies typical for internal combustion engine, the main constraint being thermal efficiency."
Though it's true that Otto & Diesel engines can have a higher max temperature due to their briefer combustion, and that the combustion is inside the piston-cylinder, thereby not requiring heat-conduction through a cylinder-wall, the Stirling is still more efficient, due to its ability to more closely approach the Carnot efficiency for a given temperature-difference.
Typically, with current technology, the Stirling is reported to be about 33% to 60% more efficient than the Otto, and about 12.5% more efficient than the Diesel. — Preceding unsigned comment added by 71.84.136.105 (talk) 15:59, 4 January 2021 (UTC)
- That entire section seems suspect just by the way it's written, making many assertions as if they were common knowledge without source.
- It's even more suspect considering that it's flat out wrong. Solar concentrator Stirling engines can focus light through a clear section of the shell onto an internal tungsten wire mesh - making them internally heated. As the heat is not conducted though the structural casing you have a theoretical operating temperature limit for the non-structural heat source approaching 3000 degrees Celsius - the actually relevant concerns for max temp are the tungsten wire heat source actually melting (as we all know, tungsten is known for being easy to melt), cooling the transparent section enough for it to remain strong and transparent (that's a thing, clear stuff usually turns opaque at high temperatures!), and actually concentrating Solar energy to that kind of extreme (not as easy as it sounds due to conservation of etendue).
142.186.66.67 (talk) 04:00, 16 February 2022 (UTC)
Deletion of claim that Stirlings require more expensive material.
[edit]In the section that compares Stirlings to ICEs, there's a claim that Stirlings require more expensive materials. No, the NASA Stirling installed in a Chevy Celebrity didn't use metals more exotic than stainless-steel. Stainless-steel was used for the high-temperature parts.
Here's that passage, with that claim removed:
[quote] However, Stirling engines are generally not price-competitive as an automobile engine, because of high cost per unit power, low [[power density].[citation needed] [/quote]
NASA's report about their MOD2 engine said that, with mass-production economy, a Stirling car could be priced comparably to an ICE-powered car. Sure, maybe a bit more, but not prohibitively, outright unaffordably, more. When comparing price, it's important to not forget that mass-production will cost less per unit than building a prototype.
Because of its greater efficiency, the Stirling can run a bit cooler. The MOD2 report said that, at the Stirling's max temperature, NOx emission isn't a problem.
A Stirling car has an advantage over an electric car: The Stirling, made of abundant metals like aluminum & iron (which is what stainless-steel is) doen't need the exotic scarce or semi-scarce metals that batteries & fuel-cells need. For everyone to have electric cars would likely cause disastrous environtal damage from the mining of the needed exotic metals. Iron and aluminum are very abundant in the Earth's crust.
Here's a possible disadvantage of the Stirling for a mass-ownership vehicle-engine:
One good thing about internal-combustion engines is that the combustion is enclose inside the large, heavy and thick motor-block. An external-combustion-engine's burner isn't quite as well isolated.
In any acceptable transportation/energy future, it would obviously be out of the question for the general population to own and drive the big & heavy cars that are now in use. Any personal motor-vehicles would have to be limited to low-power motorbikes & motor-scooters; and maybe tiny ultra-ultra-light cars for special needs, for families & disabled-people.
For such small vehicles, might there not be a problem protecting the fuel-tank and the driver (& any passengers) from the burner?
Well, maybe that problem could be avoided by having a V-2 or V-4 Alpha Stirling at the very rear of the motor-scooter, motor-bike, or tiny car. The crankshaft would be oriented transversely (parallel to the axles), and the hot cylinder(s) would be on the rear side of the V. In that way, the burner(s) would be far from the fuel-tank and the driver.
The cold-cylinder could be vertical, with the hot-cylinder horizontal and pointed backward.
By the way, ICEs have another huge disadvantage for mass-ownership vehicles: They're filthy. ...no matter what the fuel is. Even burning hydrogen or ammonia, there's NOx. Controllable by hang-on devices? With everyone having an ICE car, lots of people don't maintain their cars (maybe many can't afford to). The hang-on devices have to be maintained. The engine itself has to be maintained. With everyone owning & using the filthy ICEs, inevitably there will be many dirty unmaintained ones. ...all the worse when idling at the curbe or under your window, especially when they're cold. With ammonia fuel burned in mass-ownership ICEs, the air will be as full of NOx, in its many forms, and unburned NH3, as it now is full of half-burned carcinogenic hydrocarbons and particulates...and of course NOx. With hydrogen ICEs mass-owned, NOx will be thick.
So I suggest that ICEs (Otto & Diesel) are completely unacceptable for mass-ownership, no matter what the fuel.
- @71.84.136.105: it all comes down to sources. If you can provide verifiable references for the statements you want to include, that is suitable material for the article; otherwise it can't be used. Personal reasoning, synthesis, or arguments based on personal knowledge without a print source to back it up are not usable here. --Elmidae (talk · contribs) 22:52, 16 January 2021 (UTC)
- I know better than to try to get into the article anything that hasn't been copied from somewhere :D
- Additionally, for verification about the unacceptability of ICEs for mass-ownership, just get a whiff of the air along any busy city street, or in a low-income neighborhood during morning warmup-time. The families of the drivers have to live there.
- — Preceding unsigned comment added by 71.84.136.105 (talk • contribs) 02:33, 17 January 2021 (UTC)
Proposed explanation of Stirling cycle & the mechanisms that achieve it...for the beginning of the article.
[edit]Extended content
|
---|
How The Alpha Stirling Engine works: First a statemennt of the ideal Stirling-Cycle, and then a description of how the Stirling-engine approximates that cycle. The Stirling-Cycle: The ideal Stirling Cycle gives the max-possible efficiency for any particular max & min temperatures--the Carnot efficiency. Of course no engine can really achieve that ideal, and no engine really achieves its ideal cycle, but actual, attainable, practical Stirling engines are outstanding for their efficiency. With any heat-engine with a gas as a working-fluid (...such as Stirling, Otto & Diesel) , the air is of course heated before it expands to do work. But first it's compressed when cold, because the more it's compressed when cold, then the more space it has, through which to expand when hot (and therefore at higher pressure)--thereby doinig more work during the hot expansion than was expended to compress it. (...and that's true of all heat engines, and is the reason why our Otto (spark-ignition gasoline) engines get their best efficiency and power at high compression-ratios. ...and a reason why the Diesel is more effiient than the Otto.) The max temperature of the engine is typically limited by the temperature that the metal can withstand. The min-temperature is the lowest temperature achievable in the engine. Air at high temp has more pressure at a given volume. Air at low temp has less pressure at a given volume. So, to get the best possible work from the engine, you'dd want to expand the air at the engine's max temperature, and compress it at the engine's min temperature. (As was said above, you compress it when cold, so that you can expand it more when it's hot.) So here's the Stirling-Cycle, to achieve the above: Constant-temperature compression (at the min temperature) Constant-volume heating Constant temperature expansion (at the max temperature) Constant volume cooling The engine mechanism to approximate those four Stirling-cycle processes: Robert Stirling, a Scottish minister, in 1816, devised a two ingenious mechanisms to achieve that Stirling Cycle (to approximate the ideal Stirling cycle) for optimum efficiency, using one or two pistons and a crankshaft. Alpha Configuration: One of those mechanisms is the Alpha-Configuration, which uses two pistons. Here's how the two pistons achieve that cycle: There's no displacer. There are two cylinders. One is constantly heated to the max temp, and the other is constantly cooled to the min temp. Each cylinder contains a piston. One of the cylinders is kept hot by burners around it. The other is kept cold by a cooling heat-exchanger around it. Each piston is connected to a crank on a crankshaft, often to the same crank. They're connected to their crank(s) in such a way that the motions of the two pistons differ in phase by 90 degrees. One way is for the pistons' connecting-rods to be attached to the end of the same crank. In that configuration, the two cylinders are in a V-arrangement, a 90-degree V, with the crankshaft at the bottom of the V. The hot-cylinder is on the side of the v that the crank-tip is moving away from when at the top of its motion. The cold cylinder is on the other side of the V. So the crank-tip passes the hot piston before the cold piston, and so the hot pistion's motion is 90 degrees ahead of the motion of the cold-piston. But, conceivably the two pistons could instead be side-by side and parallel, with different cranks, on the same crankshaft, with those two cranks 90 degrees apart, with the hot-piston's crank 90 degrees ahead of the cold-piston's crank. (Sometimes there's advocacy, &/or practice, of using a different phase difference, other than 90 degrees, but the phase-difference will be 90-degrees in this discussion, because that's the standard phase-difference in the descriptions, and probably in actual use.) The important thing is that the hot piston be 90 degrees ahead of the cold piston. Say it's the 90-degree V configuration, with both pistons' connecting-rods connected to the end (rod-bearing-journal) of the same crank. So the crankshaft is at the bottom of the V. At their tops, the two cylinders are connected by a tube. At the middle of the tube is a regenerator (about which more which later), consisting of a cannister containing a stack of fine metal screens, or densely-packed steel-wool. It absorbs heat from hot air going through it, cooling that air on its way to being compressed in the cold cylinder. That heat is given back to the air when it later again passes through the regenearator in the opposite direction, on its way to be expanded in the hot-cylinder. Thereby, the regenerator reduces the amount of heat that has to flow through the engine, to do the heating & cooling of the air. So here, again, is the Stirling-Cycle that is to be implemented: 1. Constant volume Cooling 2. Constant temperature compression (at the min temp) 3. Constant volume heating 4. Constant volume temperature expansion (at the max temp) Here, it is suggested that a diagram be drawn, because this subject makes more sense when illustrated by a drawing. Below is the suggestion for making the drawing: Draw a V, with two lines about an inch or two long, which meet at a rigfht-angle at the bottom. At the upper end of each line, draw a rectangle (with long dimension parallel to the line) representing a cylinder. Write an "H" above the left cylinder and a "C" above the right cylinder. Below the V, not connected with it, on a larger scale, draw a circle to represent the motion of the crank-tip (the rod-bearing). Make that circle an inch or two in diameter. Write the followng 8 things around the circle, clockwise starting at the top: At the top if the circle, write "displace & heat". 45 degrees to the right, clockwise, from that, write "RT" (standing for "right piston at top") 45 degress clockwise from that (at the right-hand side of the circle, the "3:00 o'clock position), write "expand". 45 degrees clockwise from that, write "LB" (standing for "left piston at bottom") 45 degrees clockwise from that (at the bottom of the circle, at the "6"00 o'clock position, write "displace & cool". 45 degrees clockwise from that, write "RB" (standing for "right piston at bottom") 45 degrees clockwise from that, at the left side of the circle, the "9:00 o'clock position), write "compress". 45 degrees clockwise from that, write "LT" (standing for "left piston at top") So we'll start at the top of the circle, the top of the crank's motion, with: 1. Constant volume heating: Say the crank is rotating clockwise. There's a part of the crank-motion, near the top, when the crank-tip is moving very roughly horizontally, toward the right, during which the cold-piston is rising and the hot-piston is falling. ...of course not at exactly the same speed, but close enough to say that, with one piston going up, the other piston going down,then the air is moving leftward through the connecting-tube at (roughly) constant volume. By that opposite motion of the two pistons, the air is being moved through the connecting-tube, and through the regenerator, toward the hot-cylinder. So, at roughly constant volume, air is going through the regenerator, which is giving heat back to the air, heating it to (at least nearly) the max temp. That's the constant-volume heating. 2. Constant temperature expansion: With the crank-tip reaches 45 degrees past (to the right of) the top if its circular motion, the RT position, the cold piston (right piston) is as high up as it goes, but the hot piston is still moving down at near its max speed. Of course the right piston doesn't really remain stationary, but near the end of its upward travel, it's relatively, most nearly, stationary. So, with right piston nearly stationary, and left piston descending fast. That compressed air that has just been heated through the regenerator is now being expanded in the left-hand cylinder, the hot cylinder. The air is expanding against the hot piston, and doing work on it. As the air expands, it's receiving heat from the walls of the hot cylinder that it's in (so that it isn't being cooled by its expansion), so that the air is expanding at a constant high temperature, the engine's max temperature. 3. Constant volume cooling: As the crank moves through the bottom part of its motion, it's moving roughtly horizontally toward the left. So the right piston is descrnding and the left piston is rising. Therefore the air is being moved towards the right, in the connecting-tube, at very roughly constant-volume (because the left piston is rising and the right piston is falling). As it moves through the regenerator at constant volume (literally with no rate of volume-change when the crank is exactly at bottom), it gives its heat to the regenerator, and is thereby cooled by the regenerator, which was previously cooled by cold air that went through it. That's the constangt volume cooling. 4. Constant temperature compression: When the crank is 45 degrees past the bottom, at "RB", the right piston reaches the bottom of its travel, and the left piston is still rising at or near its top-speed. So the air, which has just been cooled by the regenerator, is being compressed in the right-hand cylinder, the cold cylinder. Ordinarily that compression would heat the air, but the cold cylinder is surrounded by a cold-surface, a heat-sink, which absorbs heat from the air, so that, as it's compressed, that air remains at minimum-temperature. Next, process #1, constant-volume heating is repeated, as the compressed air passes through the regenerator and is heated at constant volume. Then, as described in process #2, that hot compressed air is expanded in the hot-cylinder. ...at the engine's max temperature. That's how the Alpha Stirling Engine implements the four processes of the Stirling-Cycle. I emphasize that these processes aren't sharply definitely delimited by those 45-degree positions on the crank-tip circle. Each process blends with the next one, as the pistons move in their crank-generated motions. Nor are any of the processes really the ideal-processes of the ideal Stirling-Cycle. But they approach the ideal well enough to make the Stirling Engine the most efficient heat-engine. Maybe some people have devised more complex and intricate linkages that more closely approach ideal piston-motion. But I emphasize that the NASA Stirling automotive engine, which gave a Chevy Celebrity faster 0-60 time than that of the ordinary Otto Celebrity, with 33% better efficiency, used the ordinary crank-actuation of the pistions, as described above. Beta Configuration The Beta uses only one piston, to both compress and expand the air (actually, to be pushed by the expanding air). So, instead of two pistsons, it has a piston and a displacer. The piston's cylinder adjoins and open into a displacement-chamber. That chamber's walls are heated at one end (the end farthest from the crankshaft), and cooled at its other end (the end toward the crankshaft). In that displacement-chamber is a displacer, which is volume-occupying cylindrical object that fills much of the chamber's circular cross-section. The displacer fills much of the chambrer's volume. The piston is moved by a connecting-rod connected to a crank on a crankshaft. So is the displacer. The displacer's crank is 90 degrees ahead of the piston's crank, so that the displacer's motion is 90 degrees ahead of the piston's motion. The regenerator is in one or more passages in the displacer, or sometimes (as evidently in Stirling's original patent) is wrapped around the outside of the displacer. ...or, sometimes (only in table-models?) the displacer itself is made of the steel-wool, or stacked-screens, etc. and so the displacer is the regenerator. When the displacer's crank pushes it away from the crankshaft, it moves to the hot end of the chamber,thereby displacing the air into the cold end of the chamber. On its way there, the air, passing through the regenerator, gives (much of) its heat to the regenerator, thereby cooling it and heating the regernerator. Following 90 degrees behind the displacer, the piston's crank moves it away from the crankshaft, and so the piston moves toward the displacement-chamber, thereby compressing the cold air. As the air is being compressed, the heat-of-compression is absorbed by the heat-sink, the cold-surface at that cold end of the chamber. By the time that compression is complete, the displacer has begun moving back toward the crankshaft and the hot-side of the chamber, and displaces the compressed cold air back into the hot side. As the air is displaced, it again goes through the regenerator, thereby being heated and cooling the regenerator. 90 degrees of crankshaft rotation after that displacement began, the piston, too, in its turn begins moving back toward the crankshaft and away from the chamber. As the heated air expands behind the retreating piston, the heat that it receives fromt the hot surface of the hot-cylinder keeps the air at its max temp during that expansion. ...and so on. The regenerator moves the air back and forth between the hot side and the cold side of the displacement-chamber, thereby cooling it and heating it. And, 90 degrees behind the displacer, the piston compresses the cold air when the bulk of the air is in its (cold) end of the chamber, and then moves away to expand (be pushed by) the heated compressed air that is then expanding up from the other end, the heated end, of the displacement chamber, when the bulk of the air is in the hot side of the chamber, kept hot and expanding around the displacer against the piston So the Beta uses the piston for both compression & expansion. This also requires dual-use for certain spaces. The end of the displacement-chamber has to keep-cold the air that's being compressed, but it also has to conduct, to the piston, the hot air expanding from the hot-end of the chambrer. Likewise, the regenerator passages in the displacer, &/or the space around the displacer has to heat or cool the air going through them. But they have to also provide passage for the hot air in the hot-section to expand through them. These dual-uses of those spaces result in undesired cooling of the expanding hot air, to the detriment of efficiency. But, because, when the bulk of the air is in the hot end, that's therefore where most of the expansion is to take-place, and so the cooling of the hot air expanding by the regenerator and the surface of the cold-end isn't so important, because there's less air in those spaces. ...because the bulk of the air, at that time is in the hot-space, which is large because of the displacer's position. That reduces, mitigates, the efficiency-loss due to the dual-use of those spaces, but of course it doesn't completely eliminate it. The Alpha configuration doesn't have that problem. Then why is the Beta Configuration used at all? It's cheaper to have only one (precision-fitted) piston instead of two. And with Beta, there isn't a piston in a constantly intensely heated space (as there is with the Alpha's hot-cylinder piston). Not having a hot-cylinder piston, not needing to protect the piston-seals and lubricant from the engine's max temperature likewise reduces expense. The Gamma configuration is the same as the Beta, except that, where, in the Beta, the piston & displacer are co-linear, in the same tube, thereby requiring mutually coaxial connecting-rods--In the Gamma, the displacer-chamber and the piston's cylinder are separate tubes, not sharing a central-axis, so that the connecting-rods of the piston and the displacer needn't be coaxial. NASA's MOD2 Stirling automotive engine used the Alpha Configuration. |
— Preceding unsigned comment added by 71.84.136.105 (talk • contribs) 22:07, 22 January 2021 (UTC)
HP to KW
[edit]At 700,000 lb in 2 minutes that's 1,400,000 ft*lb/min. At 33,000 ft*lb/min per HP, that's 41 HP, or 30.75 KW, right? Not 16 KW or 21 HP. 2603:7080:7006:67D3:5197:4559:7896:2EF (talk) 22:46, 1 January 2022 (UTC)
STIRLING ENGINE, STILL JUST AN IDEA!
[edit]When we use the term "Stirling Engine" we must strictly distinguish whether we are referring to the heat engines built and patented by Robert Stirling or we are referring to Stirling's idea of a Heat Engine which should operate between two isotherms and two isochores in the so-called Stirling's Thermodynamic Cycle !
Likewise, if we want to explain to someone what the Thermodynamic cycle is, we cannot do it using the Boyle-Mariotte pV-diagram. What is a thermodynamic cycle and how heat is exchanged and converted into work and work into heat is shown in Thermodynamics with a Ts-diagram, i.e. the relationship between temperature and specific values of entropy, volume and pressure in a working medium. Only the Ts-diagram can clearly show the difference between Stirling's and Carnot's Thermodynamic Cycle.
In addition, when explaining the term Stirling engine, it is important to note to readers that this term is massively abused by: irresponsible hobbyists, fake inventors and experts, traders and fraudsters, who sell their " thermal toys " under the name Stirling engine, even though these toys do not have not the slightest connection with Stirling's idea and the Stirling cycle. The same can be said for all the illustrations and animations that mistakenly try to explain to Wikipedia readers what a Stirling engine is and how it should work.
It is even more important to note to the readers that Robert Stirling never realized his ingenious idea of the construction of a heat engine with heat regeneration of the working medium "at a constant volume"! Neither Stirling nor the later builders of the so-called Stirling engine did not solve the problem of guiding the machine elements at a constant volume, but remained on improvisations (it turned out that constant volume is not so easy to control!), which led to the misconception that the problem was solved! Without further ado, this is how I imagine the content of this page (https://austav.eu/stirling.html). Just an idea? Vjekoslav Brkić, Osijek. 89.201.254.27 (talk) 17:38, 5 February 2023 (UTC)
Please get another picture
[edit]The picture is terrible as it obscures the very parts we need to see to understand how a Stirling engine works. It is made even worse by the fact that it is the first thing one sees when googling Stirling engine. Earth deserves a better intro to this subject. 23.115.207.161 (talk) 11:20, 6 May 2023 (UTC)
Oil & Gas Wells as heat sources
[edit]It is recognized that exhausted oil and gas wells present problems, but many such wells provide a heat source, because the temperature deep in the well is generally quite a bit higher than the temperature at the surface. This temperature difference can be used to power a Stirling engine, so as to provide a source of electricity. I am in Alberta, and there is sporadic interest in utilizing abandoned wells in this way. I would like to see this idea discussed in an article, with a view to the value of many small power production sites. It is reasonable to power a farm or heat a home, using Stirling technology. Janice Vian, Ph.D. (talk) 16:14, 8 July 2023 (UTC)
Regenerator
[edit]I edited the leading description to distinguish between the working piston and the displacer. The next paragraph talks about a regenerator, which is not clear enough to judge whether it's true, because I can't tell what it's talking about. As far as I know my stirling engine has no regenerator that stores heat for more efficiency, unless we're saying that the hot side of the engine does not need tool cool down and heat up again because the fluid is moving rather than the flame. 2.100.227.229 (talk) 11:25, 1 May 2024 (UTC)
Ross Linkage
[edit]While the relevancy is debatable considering his chief contribution is the linkage design and the source would need fixed if not improved, Ross' work on alpha designs featuring the linkage has been cited by other sources for Stirling engine design, and I've seen multiple vendors with low-temperature beta designs marketed as novelties that are described as having Ross linkages, so I think it's safe to say his contribution is broadly recognized and its inclusion is not promotional. Proposing a removal or re-source. SoundwavePS (talk) 12:54, 27 June 2024 (UTC)
- B-Class level-5 vital articles
- Wikipedia level-5 vital articles in Physical sciences
- B-Class vital articles in Physical sciences
- B-Class Technology articles
- WikiProject Technology articles
- B-Class physics articles
- High-importance physics articles
- B-Class physics articles of High-importance
- B-Class energy articles
- Low-importance energy articles